Kelp is on the way (KIOTWay)
Too long; didn’t read (TL;DR)
For my senior project in the fall of 2021, three of my peers and I aimed to make a contribution to a relatively unknown field: kelp farming. With the help of researchers from Oregon State, we set off to design a product that could make kelp farming operations more scalable in coastal waters through reducing human involvement, improving monitoring of kelp growth, and an actuation method that would simplify harvesting.
We utilized set based design to come up with a novel way of farming kelp: a textile, impregnated with sporophytes (baby kelp), coupled to a mechanism that would raise the grown kelp to the surface of the water where it could dry before harvest time. Drying the kelp at sea reduces its mass by 90%, allowing a farmer to optimize the number of trips they make out to the farm.
For our mechanical design we settled on a pneumatic system that would fill inflatable buoys and raise the kelp to the surface. We also added pressure sensors to help detect the depth of the farm, opening up the possibility of implementing closed-loop depth control. In three weeks, we built the system out of aluminum extrusion and sheet, laser cut acrylic, and 3d printed parts. The final product was able to float on a body of water and inflate the buoys without any leakage.
Be sure to read on, and check out the photo gallery at the bottom of this page.
Problem definition
This was the hardest part of our project, in my opinion. Nailing down a meaningful, achievable, and concise problem in a field that our team was unfamiliar with was a much larger challenge than we had expected. The world of algae farming is vast. We considered tackling issues with kelp as a method of carbon sequestration, the design of terrestrial red algae farms, and issues with farming brown algae off short. After speaking with experts in the field from Oregon State, we settled on targeting offshore brown algae farms.
We then began to craft the persona we wanted to target: a farmer looking to make more money off of their kelp farm, through scaling and optimizing the operation of their farming process. We settled on the following problem statement:
“Kelp is on the way aims to design a product that makes kelp farming operations more scalable in coastal waters through reducing human involvement, improving monitoring of kelp growth, and an actuator that makes it easier to harvest kelp.”
Ideation
Now that we had a problem to solve, it was time to ideate. In class, we learned about tools such as set based design and decision matrices, which we kept in mind as we began to build out our widest set of ideas: set A. We focused on three specific categories: actuation, monitoring, and data readout. Our final product would be a combination of ideas from these three categories.
As we moved towards narrowing down our set A ideas into set B ideas, clear trends emerged. Our ideas were falling into three categories: small devices to monitor kelp growth, devices designed to augment the way kelp is currently grown, and devices designed to revolutionize the way kelp is grown.
We met as a team and considered our options. When crafting our set C, we wanted to have a good balance of ambitious and achievable ideas. We settled on a clip-on sensor suite, a long-line buoy with sensing capabilities, an autonomous underwater vehicle, and a “textile matrix”, a farm that could grow kelp in a new and possibly more efficient way.
After meeting with our sponsor, we settled on the “textile matrix”. We based our decision on our problem statement. We wanted to make an impact on the scalability of kelp farms, and we felt that the textile matrix was our best shot at achieving our goal. Our direction was set, we were going to build a proof of concept of an entirely different way of farming kelp.
Design
Our concept was simple: by growing kelp on a textile we would be able to bring the kelp to the surface of the water where it could dry, making the harvesting process significantly easier. Dry kelp is up to 10 times lighter than wet kelp, so farmers would save time and money spent on harvesting trips. We would also be able to monitor and control the depth of the farm, allowing farmers to make remote adjustments based on conditions such as temperature and salinity.
Our set C design had assumed we would be able raise and lower the farm through a ballast system. Knowing this would be very difficult to implement in such a short time and on a $320 budget, we switched to a compressed-air system that would let us change the overall buoyancy of our farm by filling or bleeding sacs of air using a SodaStream cylinder.
Realizing our concept would be difficult. We knew we would need to prioritize making the build process as easy as possible by using design for manufacturing techniques. Our design would use 3D printed parts and adhesives only when necessary and prioritize easily accessible materials such as sheet metal, extrusion, and laser-cut acrylic.
One of the main contributions I made to the design of our farm was the inflatable buoys crafted from beach balls. Creating an inflatable sac that was air and water tight but also able to be rigidly attached to a frame was a tough engineering challenge. I came up with an idea that leveraged previous experience I had creating liquid-tight tanks for resin-based 3D printers. I realized that we could build a buoy around a hemisphere of beach ball material sandwiched between an aluminum ring and a piece of acrylic. The top of this acrylic could then be attached firmly to an aluminum extrusion. The clamping force, combined with some caulk, would create a tight seal and allow us to have a rigid mounting surface with a flexible sac for inflation.
We headed to the makerspace, armed with the blueprints to build our first prototypes of our buoy-inflation system.
Build
Building our farm was the easiest part of this project. Our team was full of hard working engineers with practical fabrication know-how. Most importantly, we had put a lot of thought into how our product would be assembled when we designed it. This was not only important for us, but also the farmers that would use our product.
We started by building a proof-of-concept buoy. It took us about an hour to make, and our first test showed that our design was air-tight, after a little bit of leak testing. This was a huge win for our team.
We weren’t home free, though, as we immediately discovered an oversight with our design: the pneumatic source. We had decided to use a SodaStream tank as our source of pressurized air, without checking to see how much pressure each tank was under. Needless to say, none of the equipment we had purchased for our pneumatic assembly was rated for the 3600+ PSI in the tank. Strapped for time, and after talking with our team and our sponsors, we decided to limit our scope to use a source of compressed air external to the farm, for both safety and to get the project done on time.
Coming off the back of a frustrating pivot, we kicked into gear to finish the rest of our hardware. We built a frame from extrusion and waterjet aluminum. We built more inflatable buoys, and routed ¼” NPT tubing throughout our farm. Finally, we assembled the electronics box and attached a textile to the top of the farm. We were ready for testing.
Late on a weeknight in the Tufts makerspace, we ran our first inflation test. We hooked up a 100 PSI compressor to our main control solenoid, and successfully inflated all four buoys. After verifying that there were no leaks, we celebrated!
The next week, we took the farm out to a local beach for the real test: could it float, and for how long? We were easily able to transport the farm and assemble it on site with only one hex key. It was nice that the thought we put into modularity and assembly paid off. As for whether it could float, the answer was yes, and for a very long time. The only reason we didn’t let it float all day was because of our freezing feet. Unfortunately, since we were using a compressor as our air supply, we couldn’t test the sinking and floating mechanism that day. Going forward, we hope to test the inflation mechanic with the farm in the water.
Takeaways
Problem definition and pneumatics are hard.
Set based design is great.
Teamwork has the word “work” in it for a reason: you have to make an effort to leverage your team’s strengths.
This project was a great way to cap off my senior fall, and I look forward to possibly revisiting it down the road.
Special thanks to Jeff, Gus, and Ray for their tireless work and superb camaraderie. Thanks to Chris and Bryony for an awesome semester.
Contact me if you like what you saw and want to talk kelp.
Photo Gallery
Photos that didn’t make the main page.
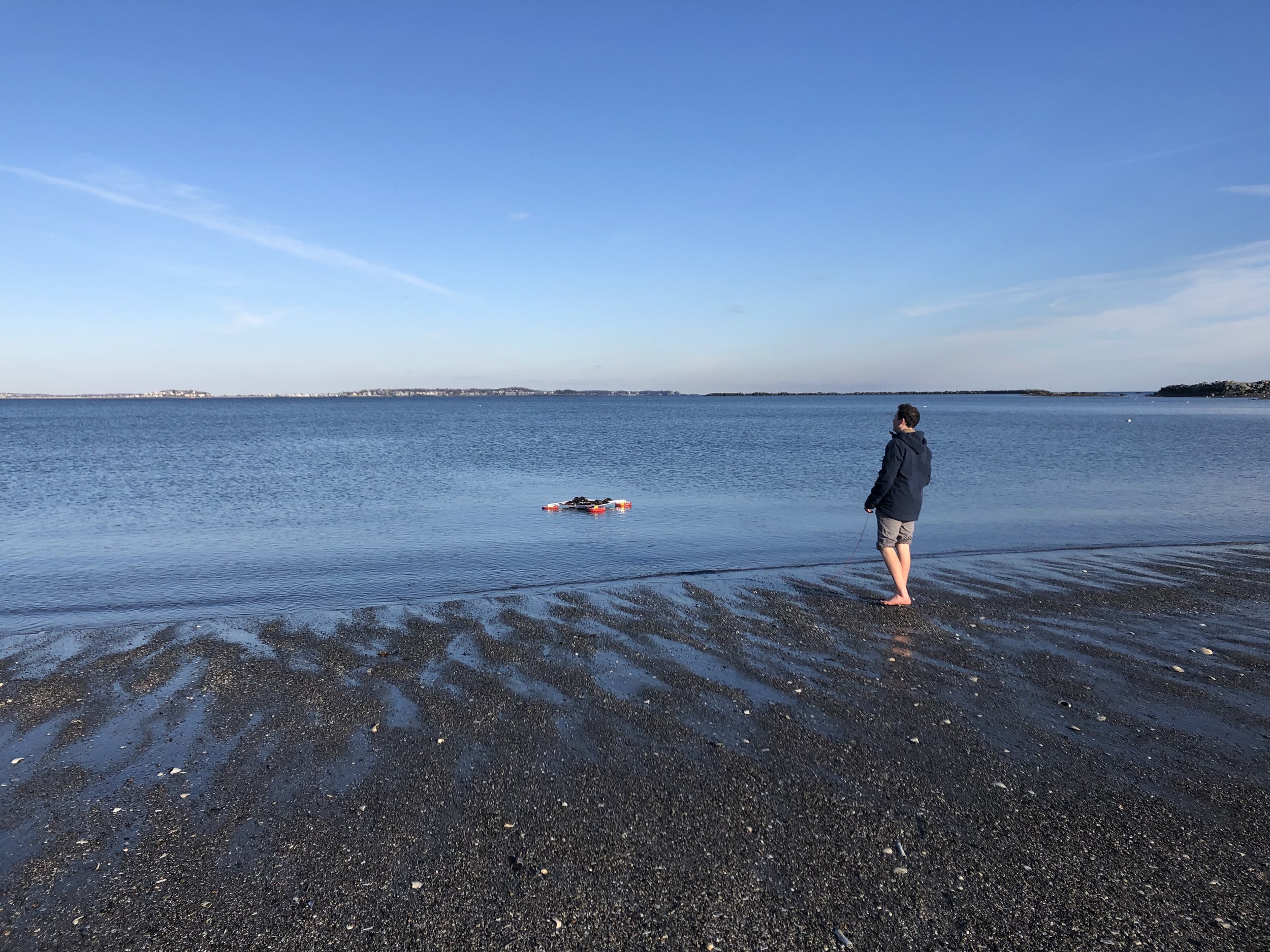
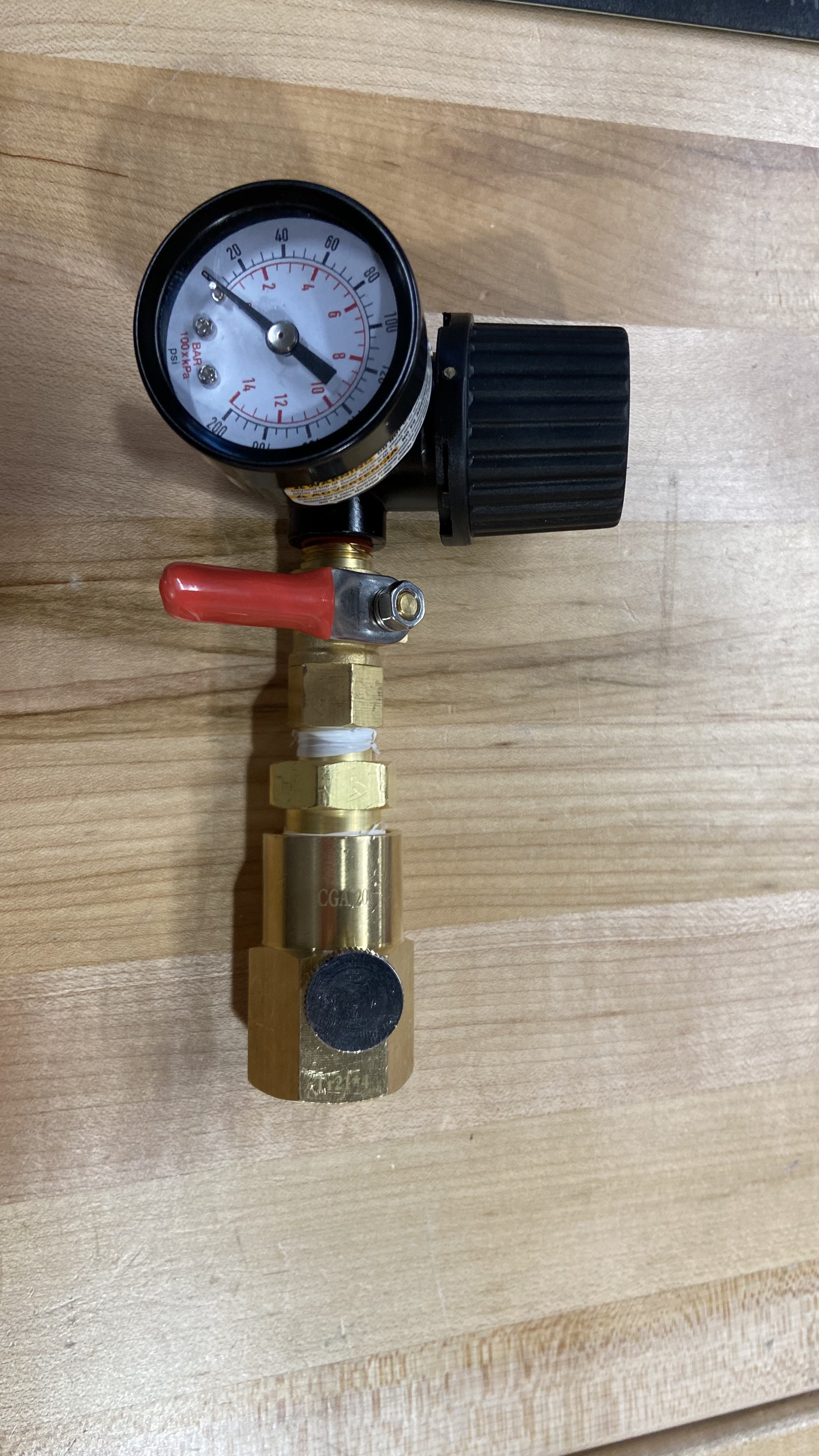
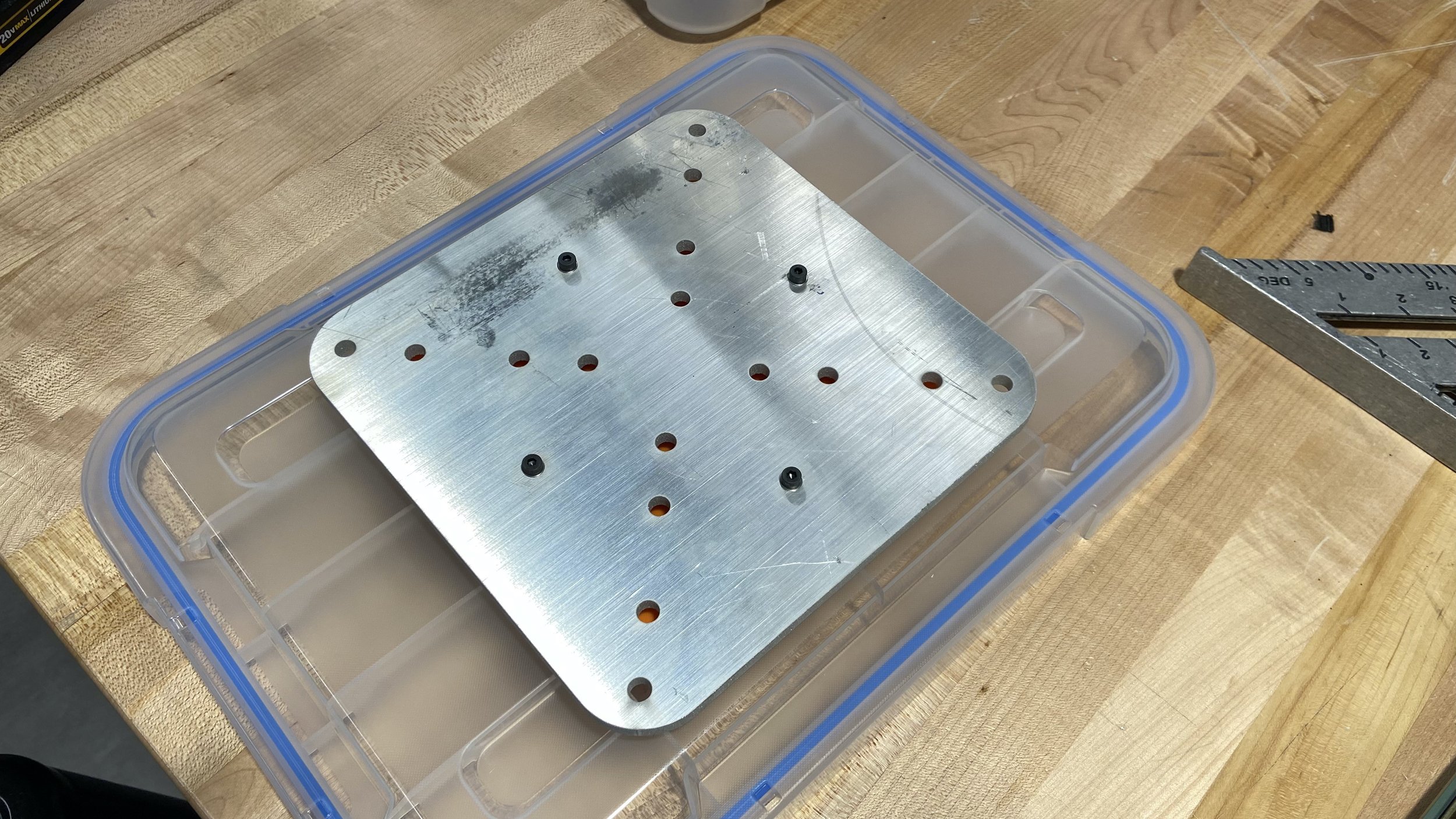
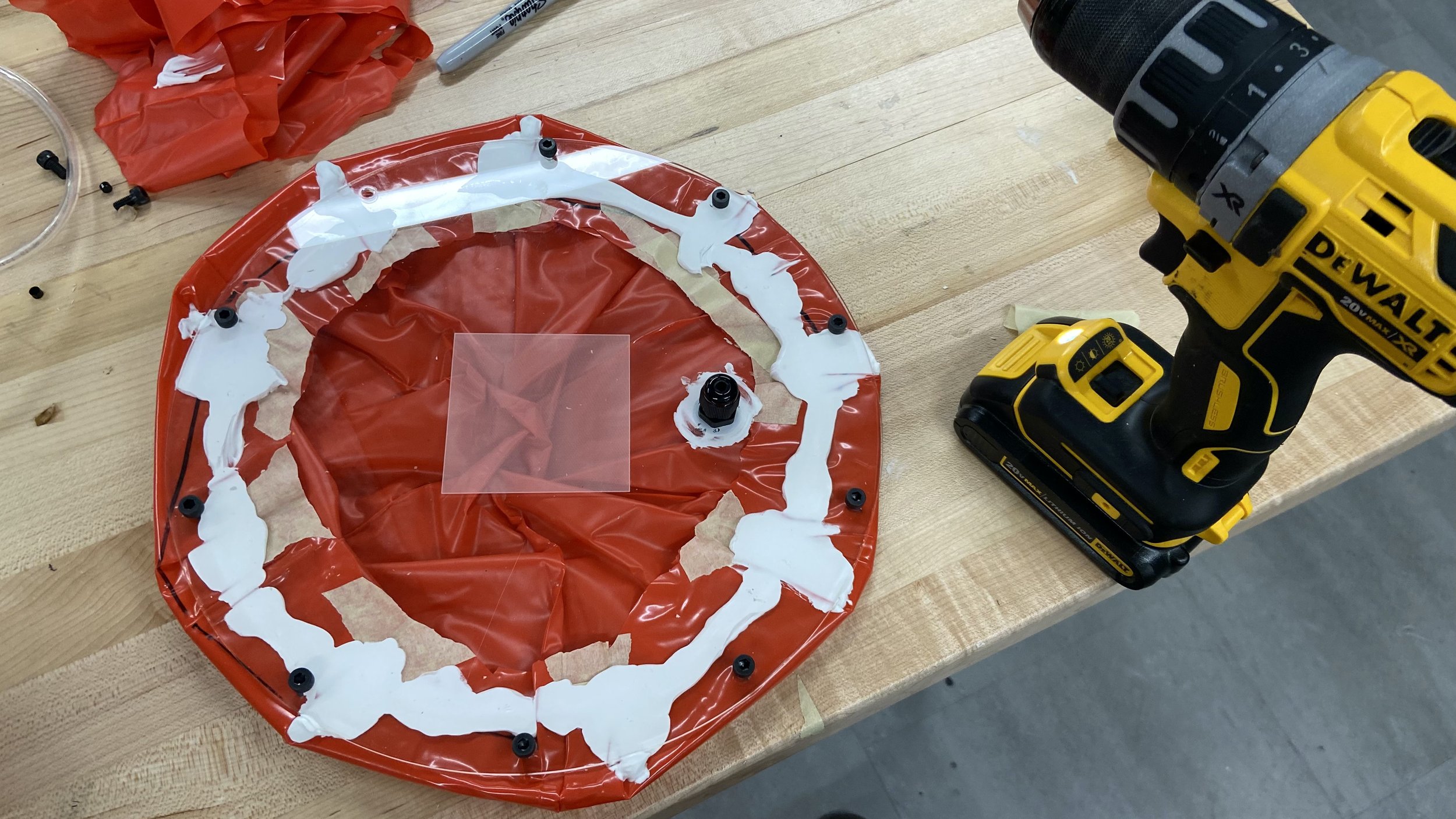
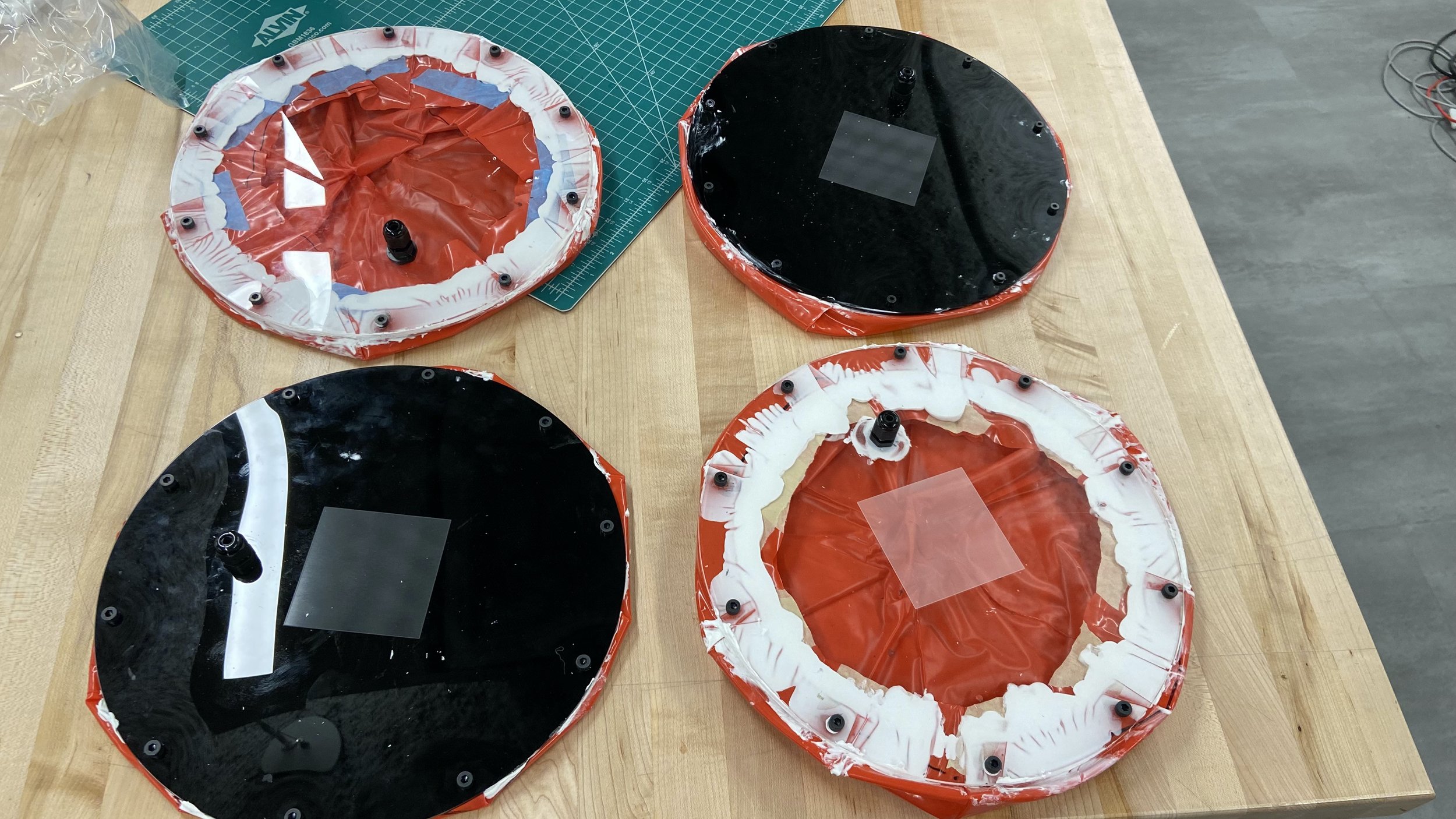
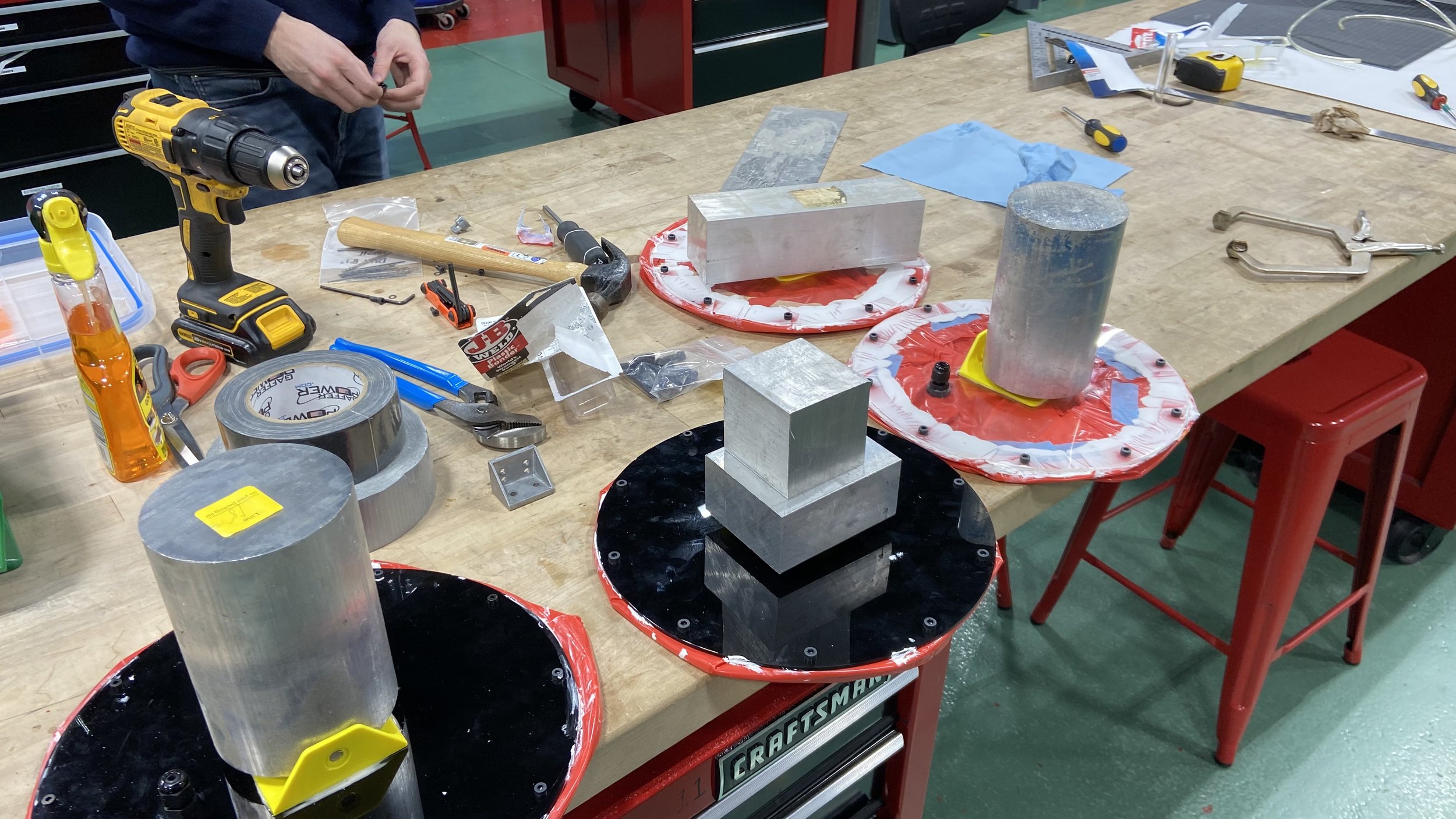
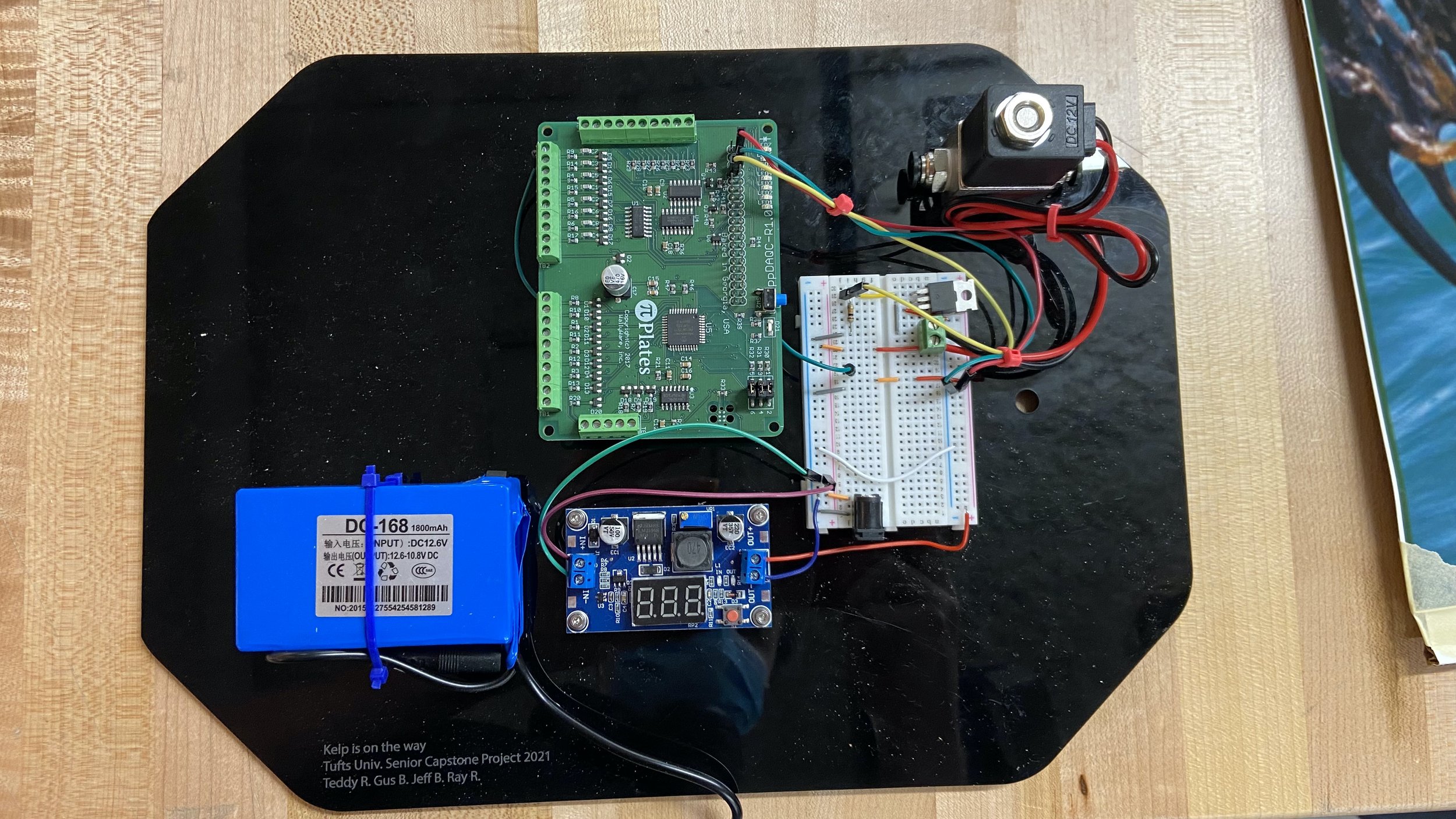
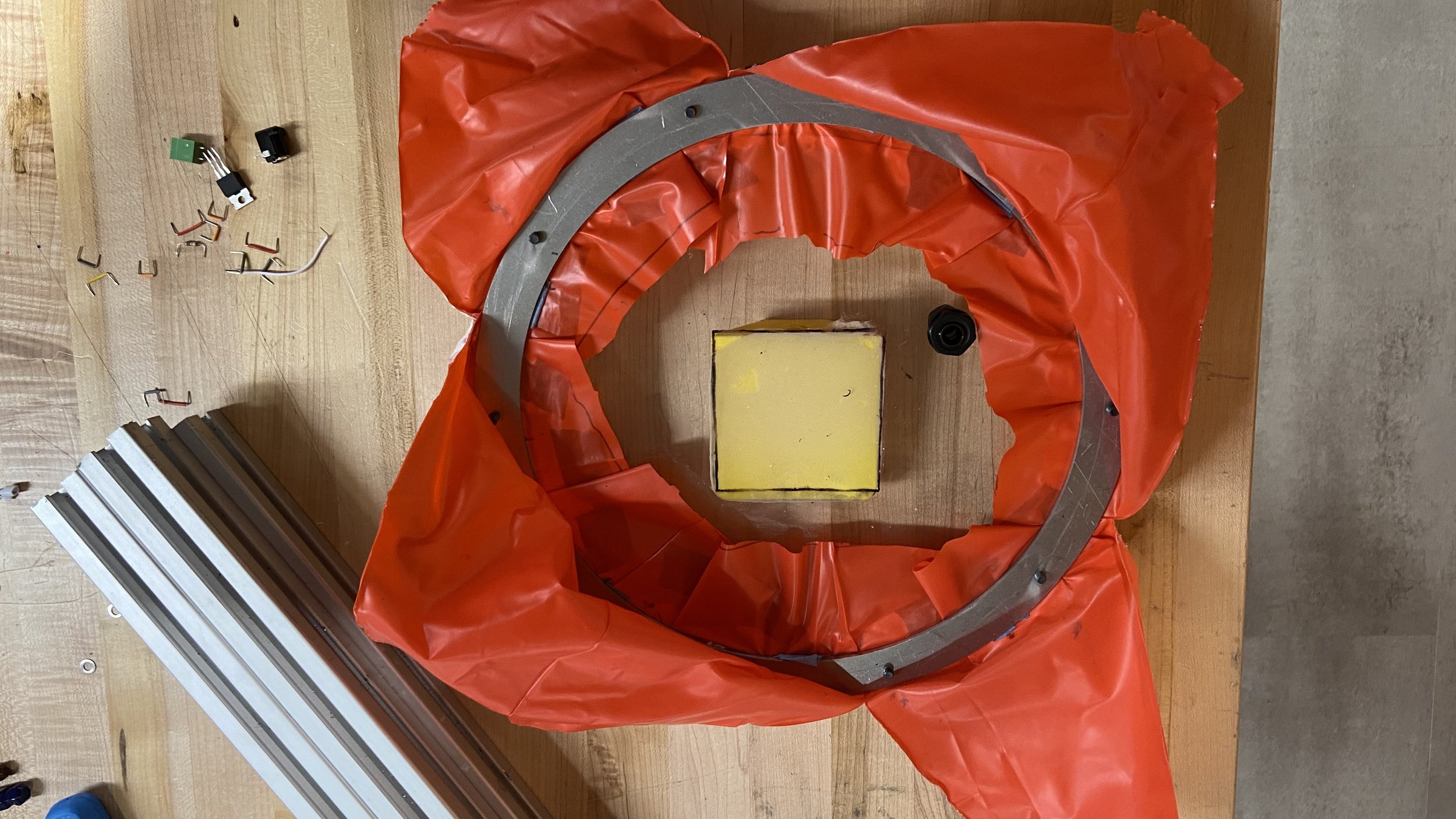
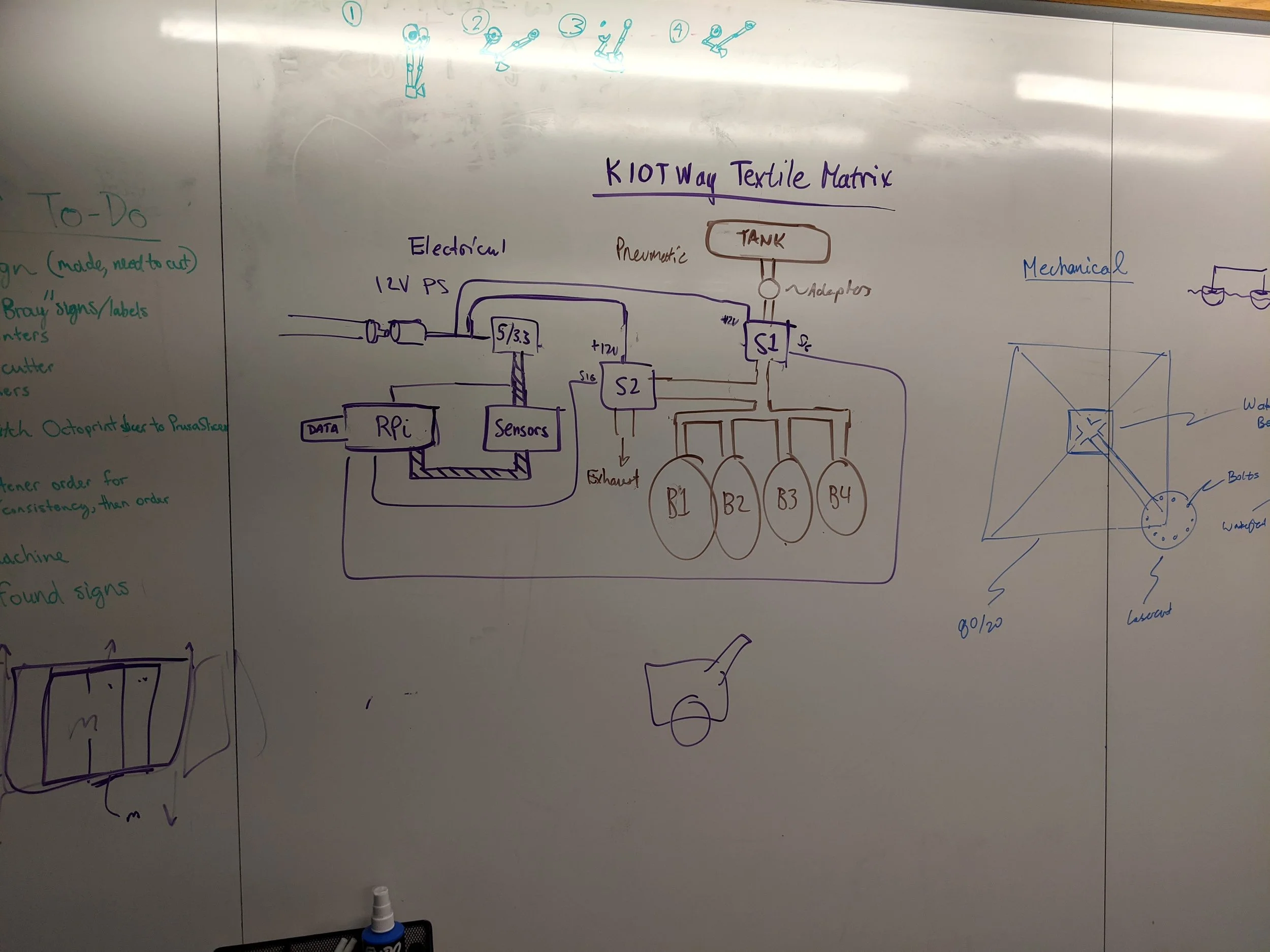

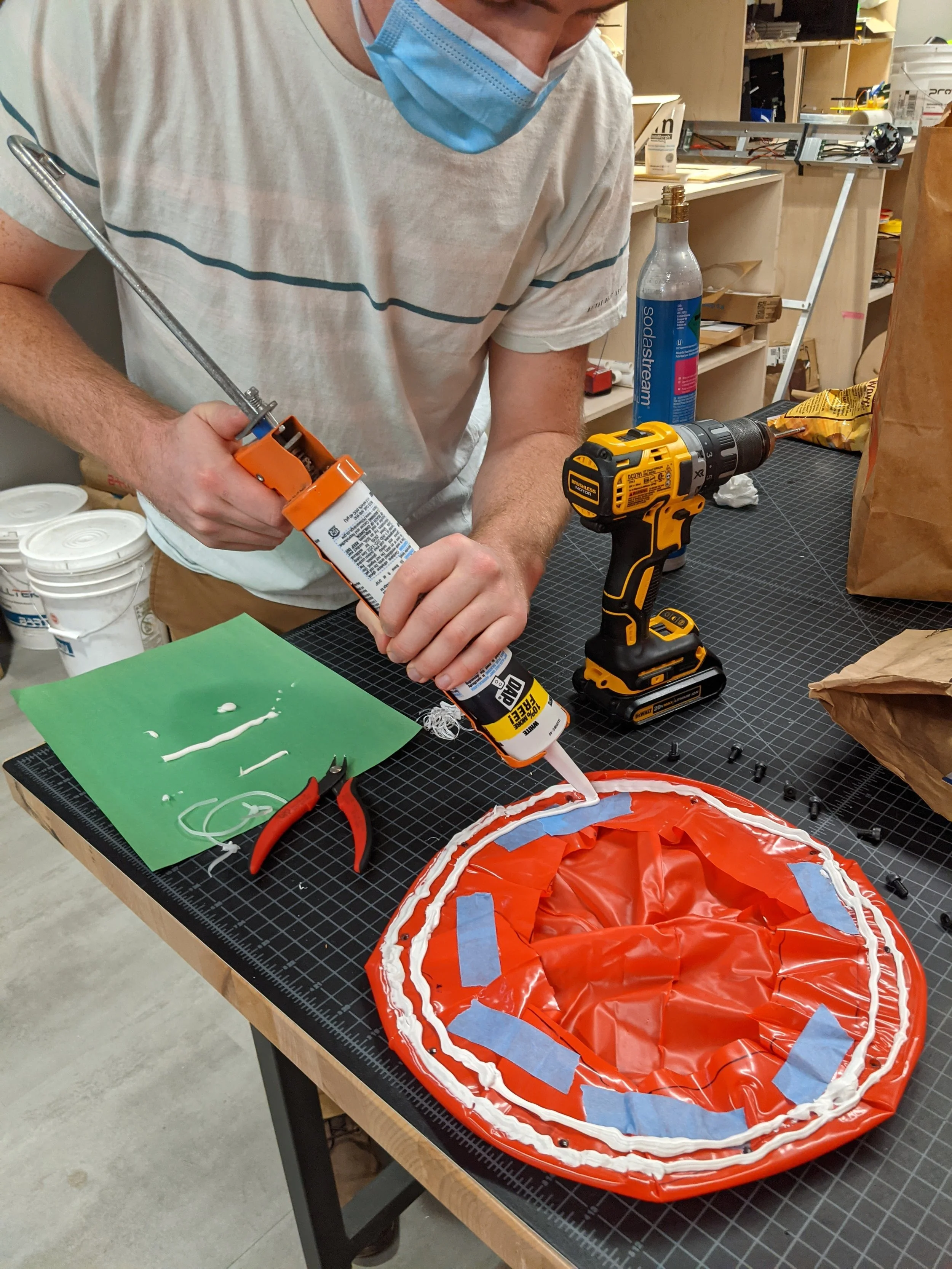
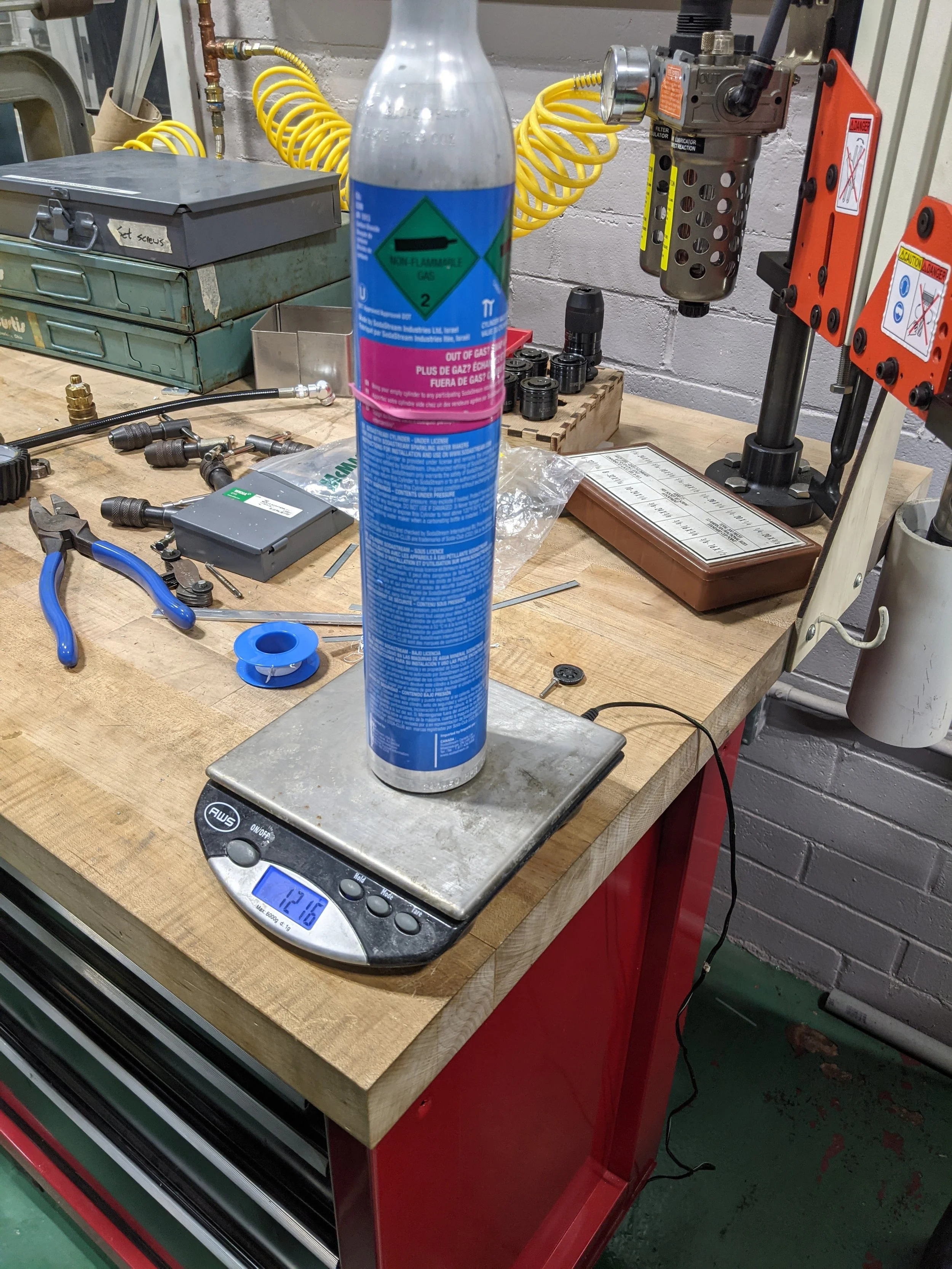
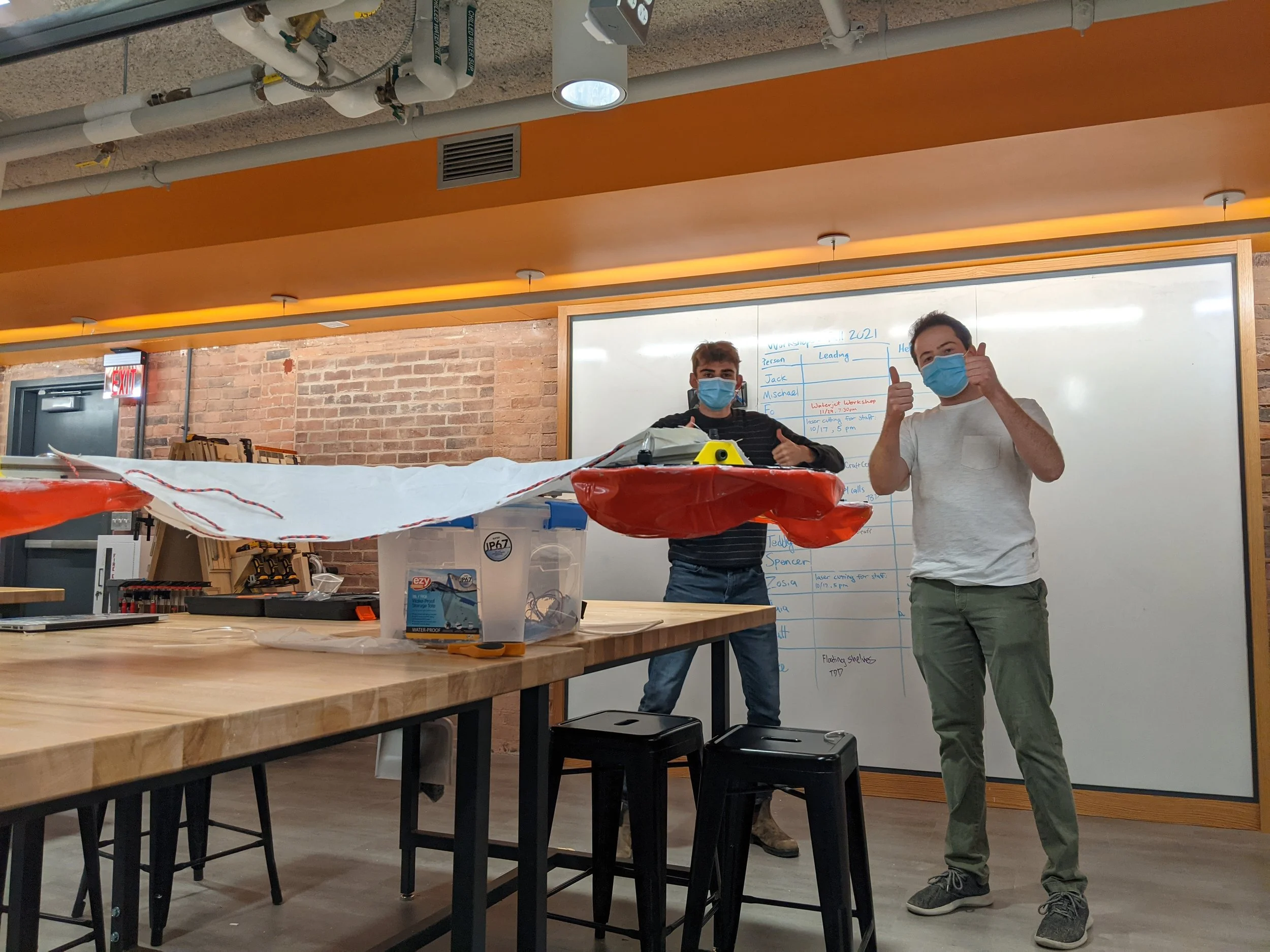

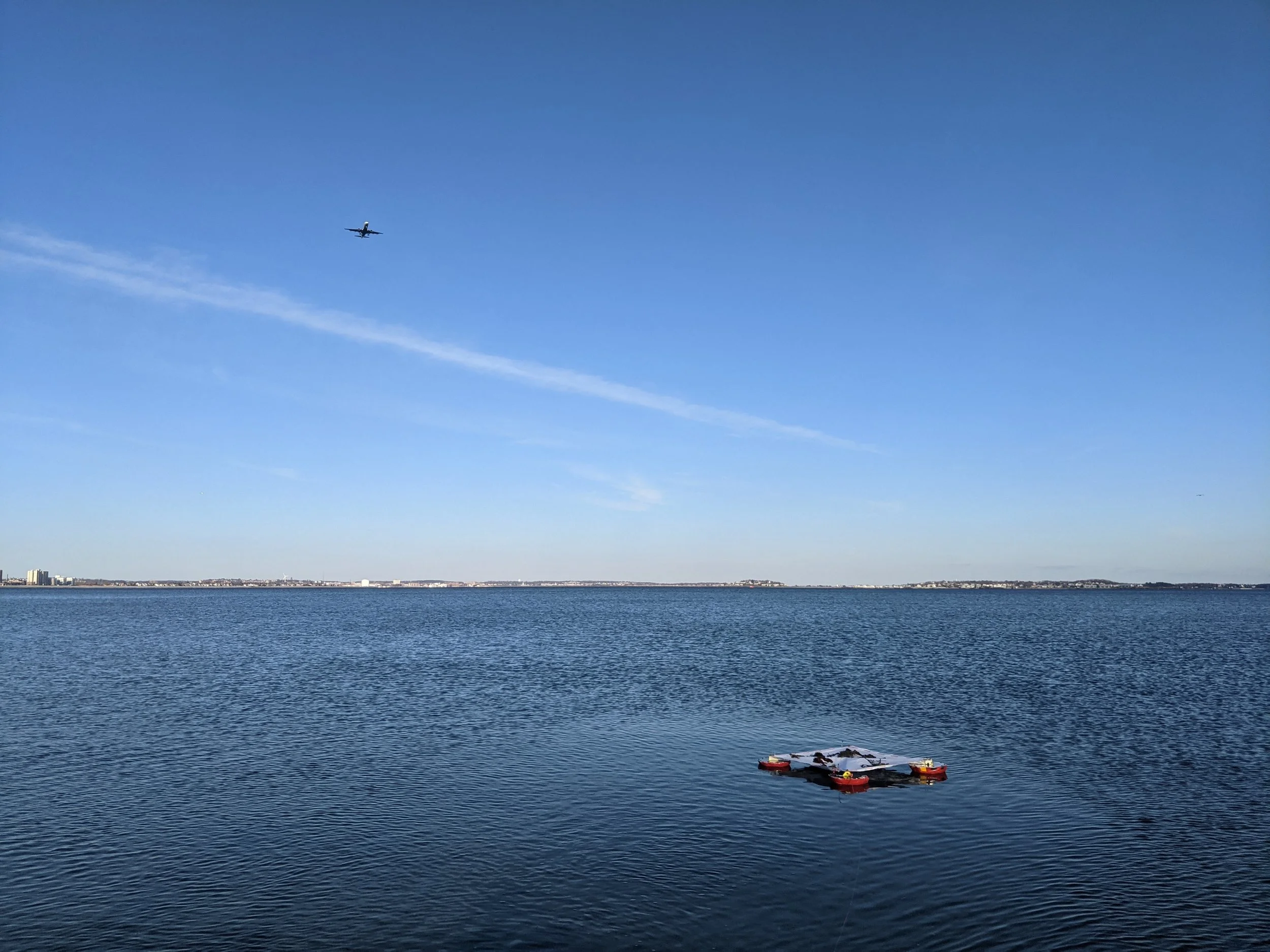